Structures today are conceived from experience, mathematical description of mechanical behavior, experimental and numerical modelling, and are a result of a complex interaction of economical-, building performance- and infrastructural optimization. Automation and digitalization will possibly lower the dependency on large industrial manufacturing infrastructure and create structural customization for specific local climatic and loading condition (Section 2). It will thereby decrease resource consumption and increase the sustainability account of the construction sector. The interface between local loading conditions (climatic, natural forces, function, dead weight) and the construction material (primary material consumption, transport, manufacturing, waste) is the structural design (Figure 2). ‘Climate&Structures’ aims on the creation of climate-oriented structural designs, i.e. resource conscious structures that use a minimum of material to withstand extreme local climatic loading conditions using parametric and topology optimization tools.
Topology optimization
Structural optimization in terms of topology optimization can minimize the material use for a maximized structural performance within a given domain. A computational algorithm places material within a space of finite volumes at the location of high strain energy according to the given loading boundary conditions. To design structural components with this tool, a set of detailed loading conditions is required to prevent over- and under-dimensioning of the structure. ‘Climate&Structures’ uses topology optimization to create high performance structures for fluctuating loading impacts, obtained from wind tunnel simulations (Section 2.1). In Fernandoy-Bak, et al. [20], a vault-shaped structure was optimized (Figure 4-a) to withstand the stochastic loading process of wind-induced surface pressures. The turbulent structure of the simulated ABL-flow is visualized in Figure 4-b. First results indicate a common solution of the topology optimization for all loading instants [20]. This in turn could lead to a full stochastic topology optimization of the load carrying system for extreme climate impacts. Placing even inferior material strategically where it serves best structural safety and durability, will lead to a significant reduction of material consumption (Figure 2).
(a) (b)
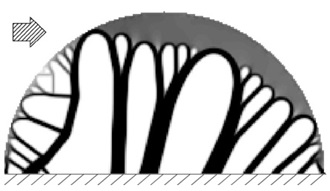
Figure 4: (a) Result from structural optimization (topology optimization) for wind loading scenarios [20], (b) visualization of turbulent flow over model in wind tunnel (flow from left to right).
Parametric multi-objective-optimization
‘Climate&Structures’ uses parametric design tools to optimize the performance of structural components. Through the inclusion of various performance objectives, the optimization process can consider not only material minimization of the structure as in Section 3.1, but include also e.g. manufacturing- and architectural boundary conditions. In Fernandoy-Bak, et al. [20], a frame-supported membrane structure has been parametrically designed for the use as an Antarctic research station. The structure was dimensioned to withstand extreme climatic loading conditions, to be transported to remote sites and assembled without mechanical help. The optimization scheme has therefore been adopted to the objectives of reaching a minimal number of structural components with limited dimensions and to create structures, being light in weight. Some of the outcomes are shown in Figure 5.
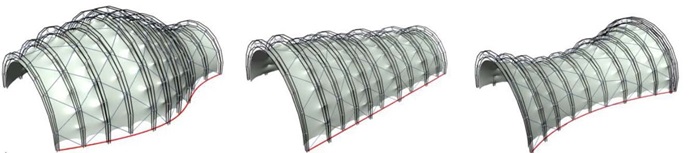

Figure 5: Frame-supported membrane structure, designed with multi-objective-optimization to withstand climatic loading impact and to fit several architectural boundary conditions. Image: [20].
Multi-objective optimizations with parametric tools give therefore the possibility, to design structural representations of climatic loading impacts, and at the same time respecting boundaries of manufacturing technologies, material resourcing, and architecture. Hence, representing the interface of all technological aspects (dark grey) in Figure 2.